top of page
WHAT IS ECONYL® REGENERATED FIBER ?
The ECONYL® fiber is not just a yarn, it represents a new way of thinking, a way of reconciling the desire for innovation with the company's ongoing commitment to protect the environment. The ECONYL® regeneration process transforms what was once waste into a new source of opportunities to be implemented in the fashion and furniture industries. Nylon waste, such as fishing nets that can no longer be used or leftovers from textile production normally destined for disposal, is recovered and transformed into a new yarn, which has the same characteristics as nylon made from virgin raw material.
It's exactly the same as brand new nylon because the fiber is repolymerized. This means that the fibers are lengthened to recreate a constitution equal to a brand new fiber.
This technique offers superior strength and quality to the fabric as opposed to other recycled fabrics that tend to be less durable.

WHAT ARE THE STEPS OF CREATION OF THIS NEW YARN?
01_WASTE COLLECTION
The ECONYL® Regeneration System starts with rescuing waste, like fishing nets, fabric scraps, carpet flooring and industrial plastic all over the world. That waste is then sorted and cleaned to recover all of the nylon possible.
There are two types of waste collected :
-
Pre-consumer : Industrial plastic waste or manufacturing scraps
-
Post-consumer : End-of-life products made of Nylon (carpets, rugs, fishing nets...)
02_PREPARATION
The nylon waste is recycled right back to its original purity. That means ECONYL® regenerated nylon is exactly the same as virgin nylon.
All the waste collected from around the world is taken to the ECONYL® waste treatment center in Slovenia, where the collected waste begins the journey back to its origins.
The different types of waste are cleaned and prepared. As part of the cleaning process,
nylon is separated from other waste and non-nylon 6 materials are removed and sent
to other supply chains. The nylon waste is cleaned, shredded, compacted and sent to the
ECONYL® regeneration plant.
03_DEPOLARIZATION
This process returns the raw material to its original state, eliminating all foreign substances for a 100% virgin quality. This is not conventional recycling, but rather regeneration, which returns nylon waste to its original form as raw material.
04_POLYMERIZATION
In this phase the ECONYL® raw material is polymerized to ECONYL® polymer.
05_PROCESSING
This is where the previously created polymers are transformed into beautiful ECONYL® yarns used for producing fabrics. It is this yarn and fabric that is then sent to our atelier in Lisbon to make our activewear.

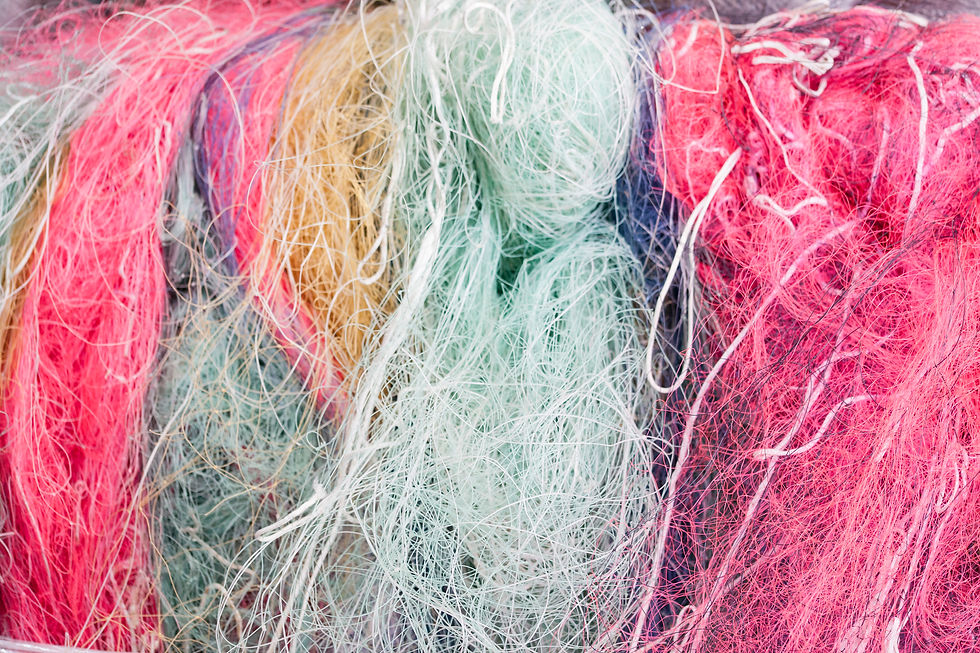
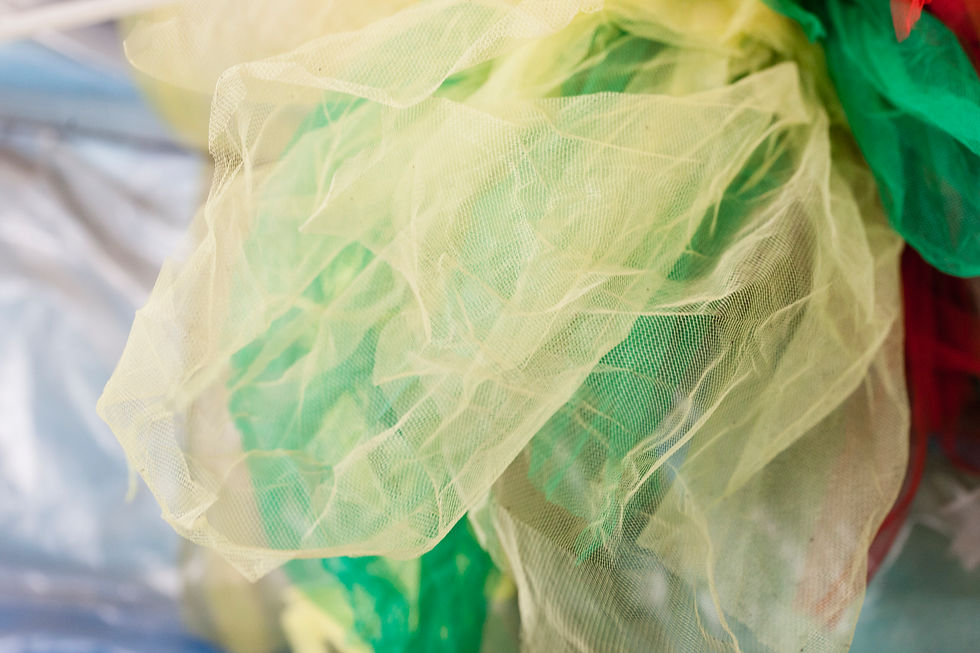

1/6




1/3
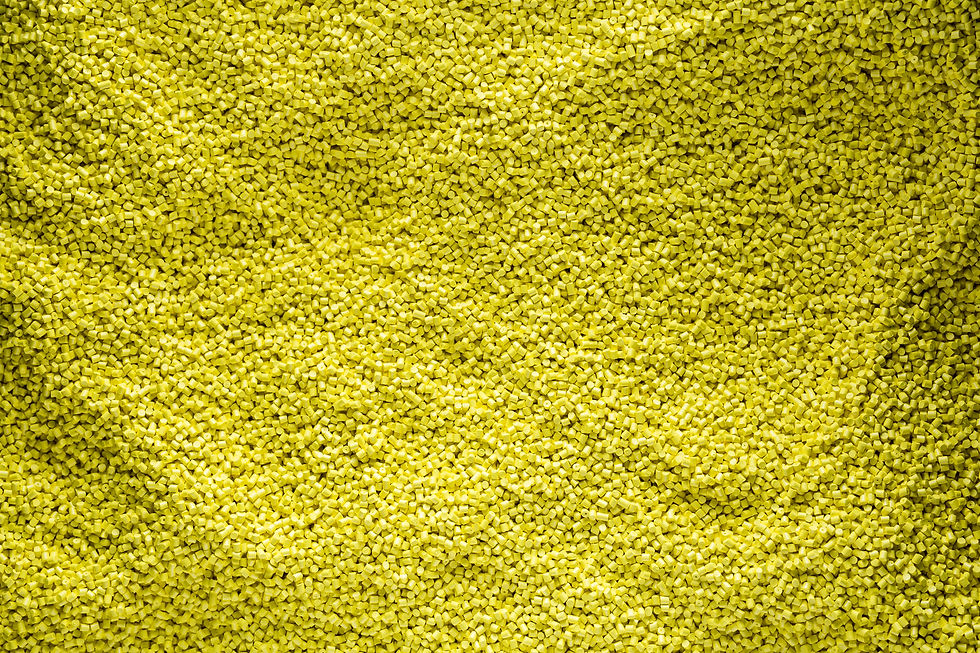
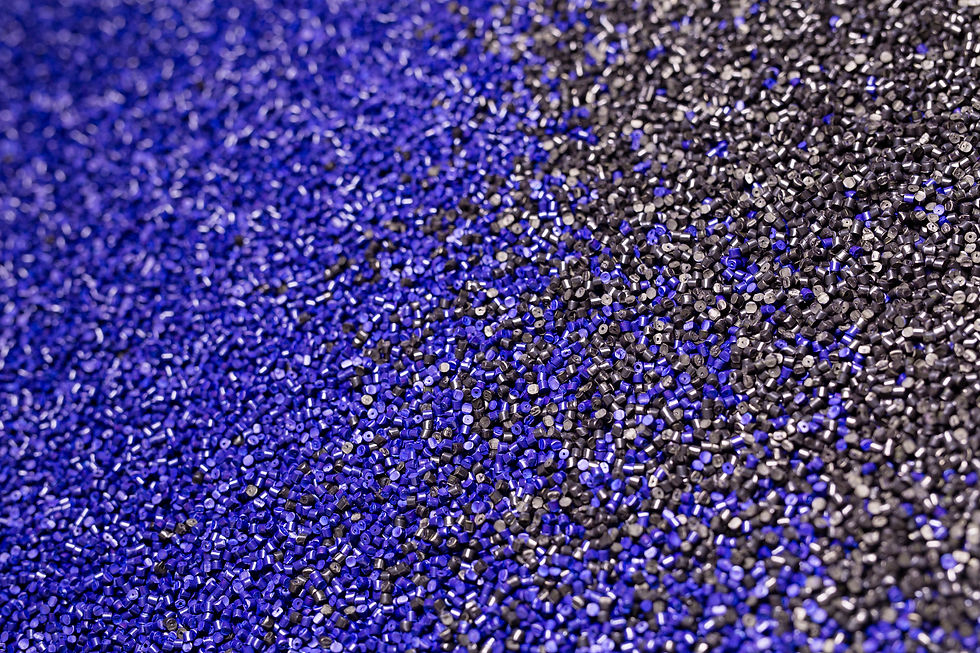

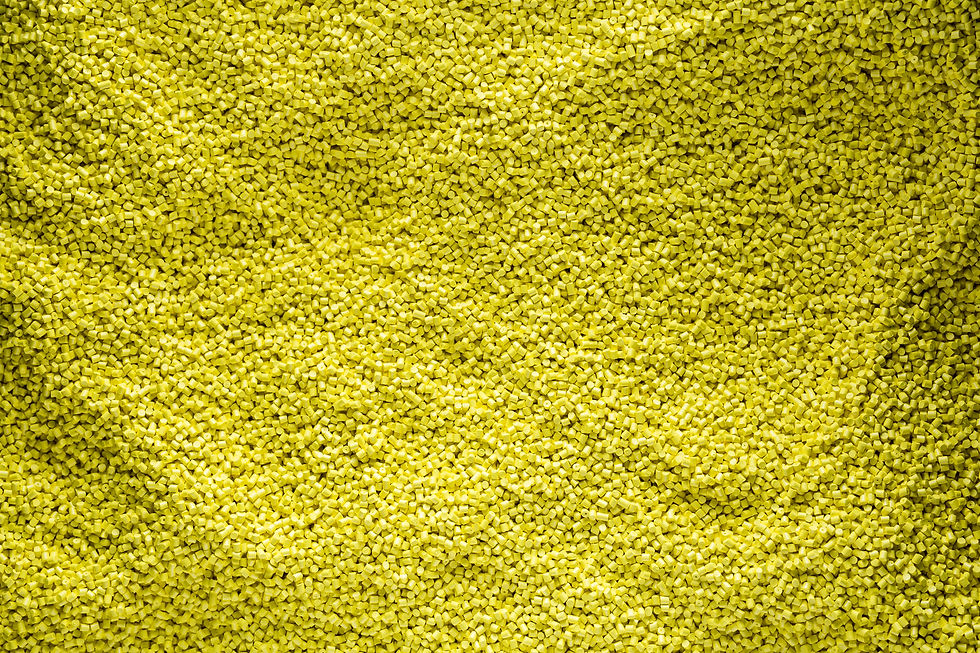
1/3
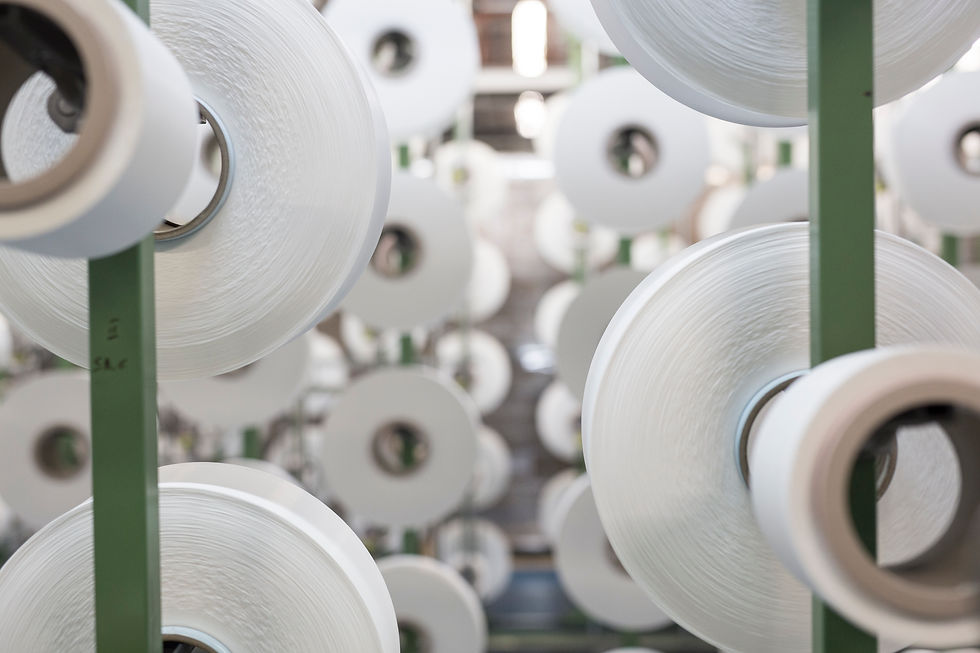
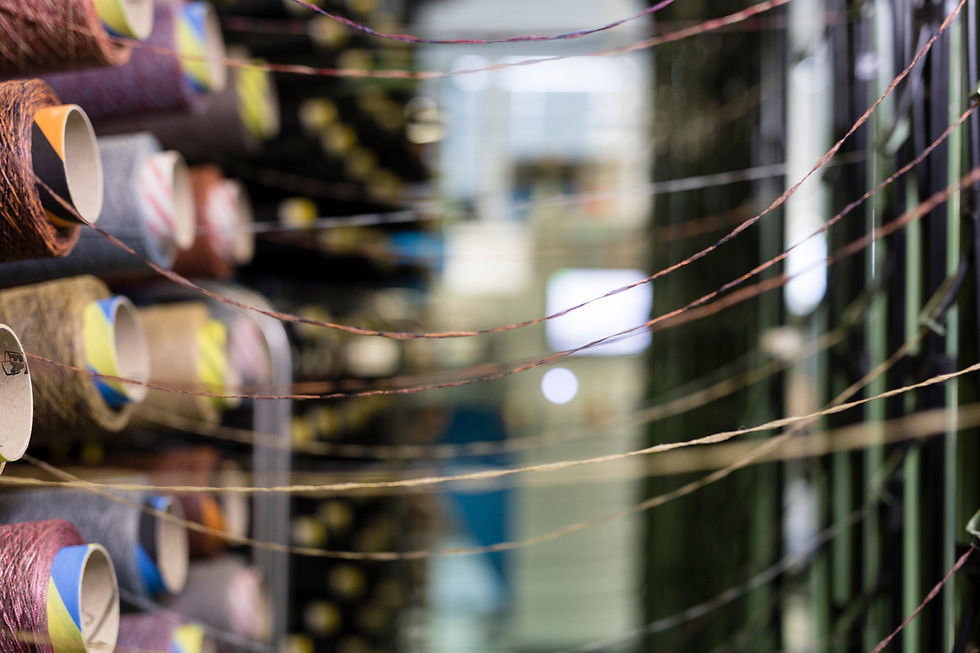
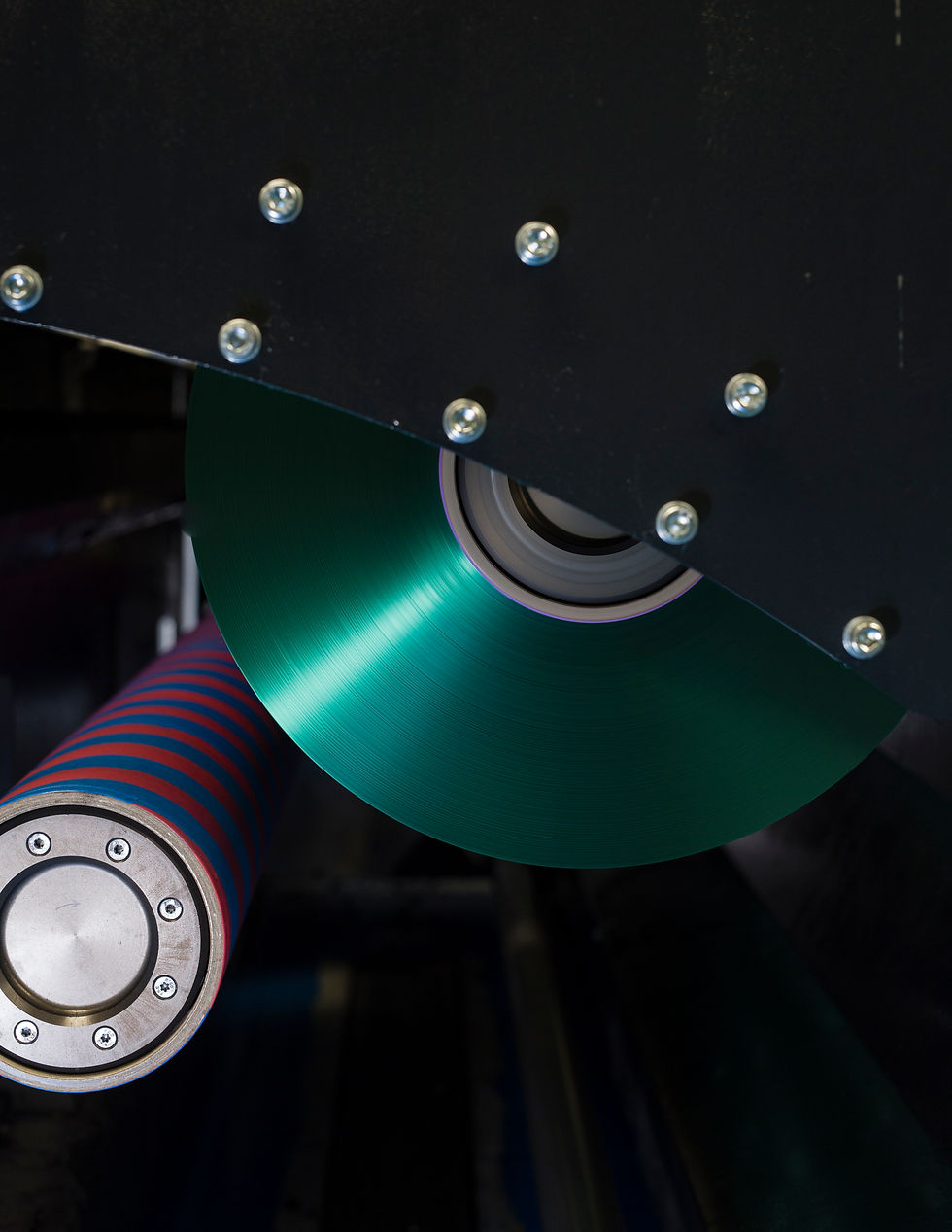
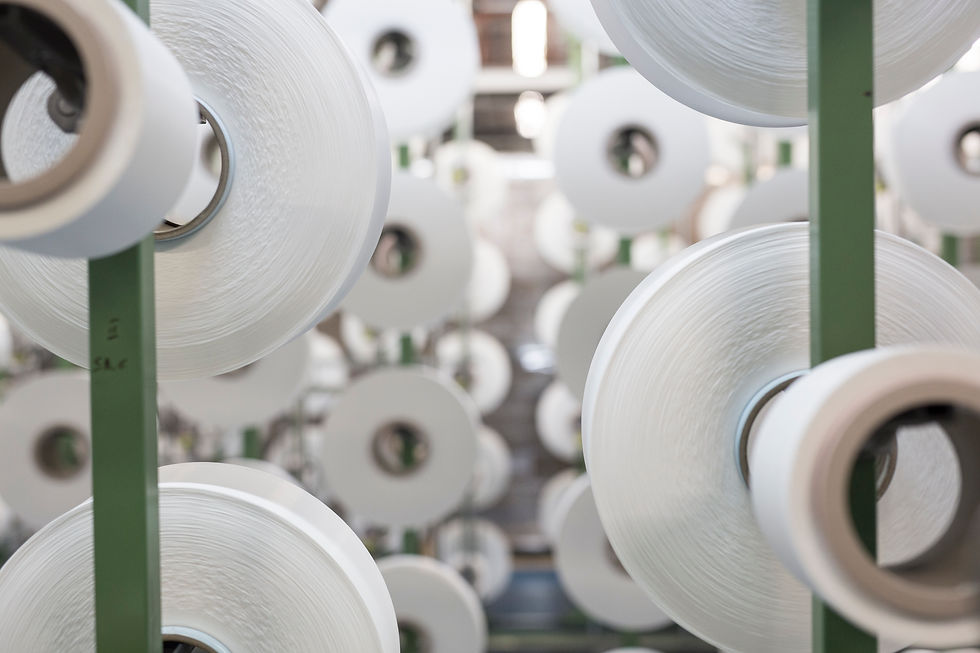
1/3
WHAT IS THE IMPACT?
The regeneration of materials saves about 7 barrels of oil per ton of regenerated polymer produced. Recycling eliminates the use of petroleum as a raw material and the traditional caprolactam manufacturing process. The manufacture of Econyl® allows a 55% reduction in CO2 emissions.

bottom of page